
Project Data
Client: Fortune 500 Global Corporation specializing in Robotics, Power, Electrical Equipment & Automation Technology
Location: Northern Mississippi, USA
Timeframe: Two Weeks
Key Project Factors: People, process and system challenges had developed throughout the facility due to lack of KPI and departmental expectations; impacting labor performance and utilization throughout the distribution operations. Without studying the activities at the elemental level, constructing multi-variable engineered standards and identifying continuous improvement opportunities, the client would have been unable to address the inefficient process and facility layout challenges negatively impacting their throughput and performance.
The Challenge
Client was struggling to get orders picked accurately within their channel operation. Similar looking SKUs being in close proximity drove errors in picking and put-away activities; ultimately driving product to be picked without verification or systemic checks. Existing standard operating procedures and systems allowed the modification of order labels without restriction impacting inventory and picking accuracy.
The Approach
CONTINUUM created predetermined order labels in client’s WMS to improve accuracy in picking processes. Implemented system constraints which required employees to verify various parts of the pick to ensure the correct product for the correct order.
The Results
Creating system-based verifications maximized picking accuracy and removed all rework previously created due to user error. By removing the opportunity for input error, the new process eliminated 100% of the inventory accuracy errors caused by the previous process. The engineered labor standards, standardization of work steps, and removal of errors from the process increased efficiency of the channel picking operation by 33%.
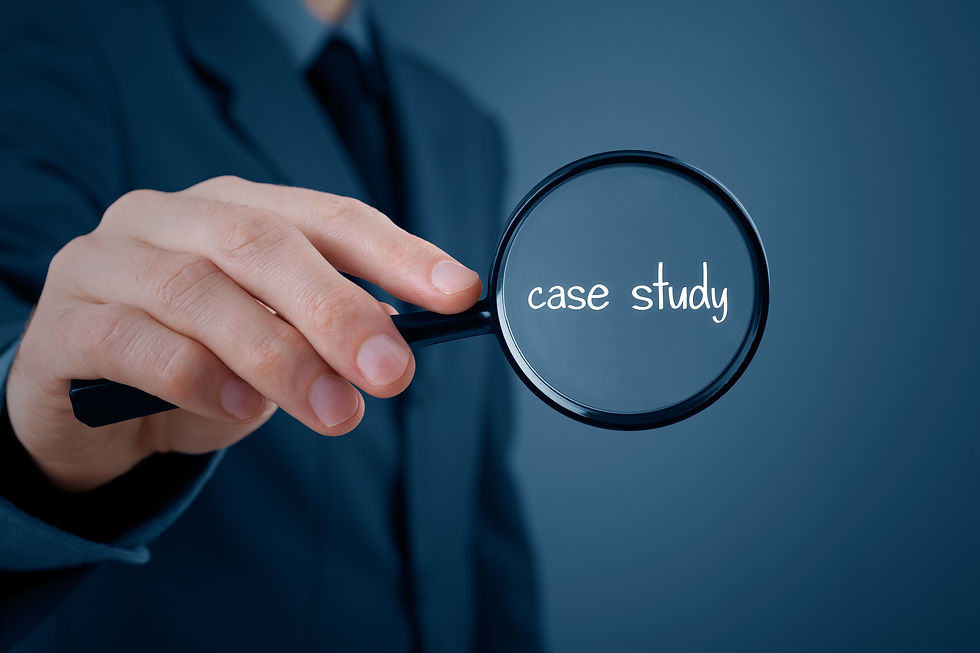