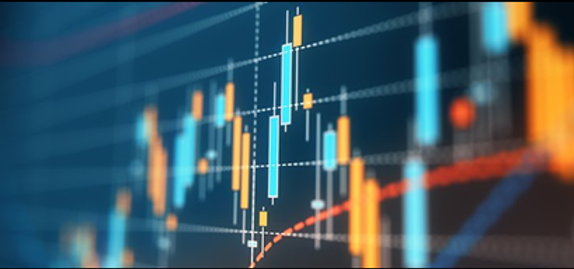
Project Data
Client: Premier North American Outdoor Sporting Goods Distributor
Location: Nevada, United States
Timeframe: 3 weeks
Key Project Factors: Management, routine, and staffing challenges were driving increased labor costs and negatively impacting productivity within the facility. Direct Augmentation of the client’s on-site leadership team and the implementation of performance management improvements was critically needed to support immediate and sustainable operational effectiveness. Continuum was tasked with ensuring business needs were achieved, operational initiatives were executed successfully and leadership teams were properly supported across the distribution facility.
The Challenge
Continuum’s client was experiencing challenges in achieving facility total labor utilization and efficiency goals defined within their labor management program and was seeing misalignment between staff planning modules and the resulting outputs as direct labor performance and utilization improved. The fact that total labor utilization was not able to be achieved even as labor utilization goals in direct functions were realized developed into a confidence gap within the facility’s LM program. Unbeknownst to the client at the time, total facility metrics are impacted not only by the output of productive operations but also the ratio of direct (productive) labor and indirect (support and off-standard activities) labor functions within distribution centers; so as less direct labor was required within the facility to meet throughput needs as productivity improved, indirect labor was not balanced to support the reduced direct staffing.
The Approach
Working with the client leadership team to understand and quantify this impact and engineer this staffing component into the program was critical to balancing overall facility labor utilization and operational efficiency. Right-sizing both direct and indirect staffing levels within LM programs is crucial as direct staff optimization through performance and direct utilization improvement will result in a decay in total utilization if indirect labor is left static. In certain operations, specific labor utilization and efficiency goals were retroactively reengineered and designed to set achievable goals based on the balance between productive and support functions within the area. Ultimately Continuum’s experts were able to help client leadership comprehend how maintaining past headcount in indirect facility functions could negatively impact total building utilization and efficiency as productive operations improved. The investigation ultimately proved that operational leadership had struggled to manage their support staff relative to their optimized direct FTEs during the program launch and resulted in a larger percentage of total hours being spent in indirect work as direct staffing was right-sized.
The Results
Continuum was able to make a immediate impact on the facility by effectively communicating the change and engineering a solution within all facets of the labor management program. Total building utilization and efficiency goals were achieved given rebalancing of indirect staff to direct labor. Once clear expectations were communicated to all leaders and employees, fair and achievable performance, utilization and efficiency goals were realigned to support continued productivity and throughout improvements across all facility operations.
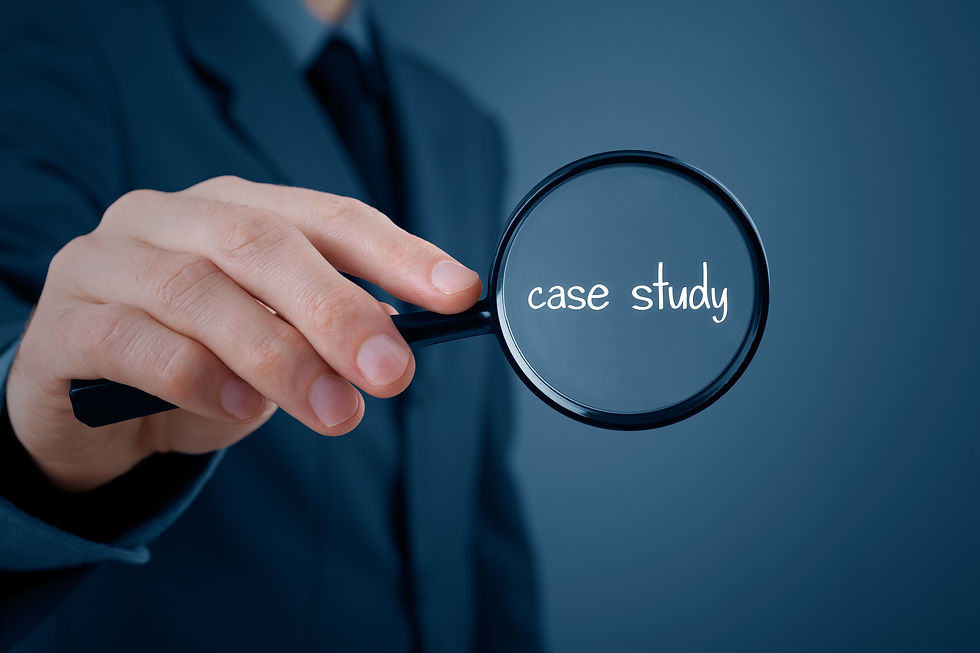