
Project Data
Client: Fortune 500 Global Corporation specializing in Robotics, Power, Electrical Equipment & Automation Technology
Location: Northern Mississippi, USA
Timeframe: One Week
Key Project Factors: People, process and system challenges had developed throughout the facility due to lack of KPI and departmental expectations; impacting labor performance and utilization throughout the distribution operations. Without studying the activities at the elemental level, constructing multi-variable engineered standards and identifying continuous improvement opportunities, the client would have been unable to address the inefficient process and facility layout challenges negatively impacting their throughput and performance.
The Challenge
Client was struggling to staff full case and split case pick modules effectively given a multitude of upstream, downstream and flow challenges. Timing issues created large swings in picking demand across multiple modules which drove extra labor and unnecessary movement of staff between operations.
The Approach
Through standard development and process evaluation, CONTINUUM identified process and system delays that drove major utilization issues in the operation. Using the data to quantify labor hour loss, the pick modules were restaffed accordingly allowing Associates in the operation to have more consistent flow of work and less movement between various modules to find productive work.
The Results
Utilization issues identified and corrected as part of this engagement led to an immediate 40% reduction in staff before engineering standard implementation. After application of performance standards, the picking department had an additional increase in efficiency of 27% through performance reporting and coaching efforts.
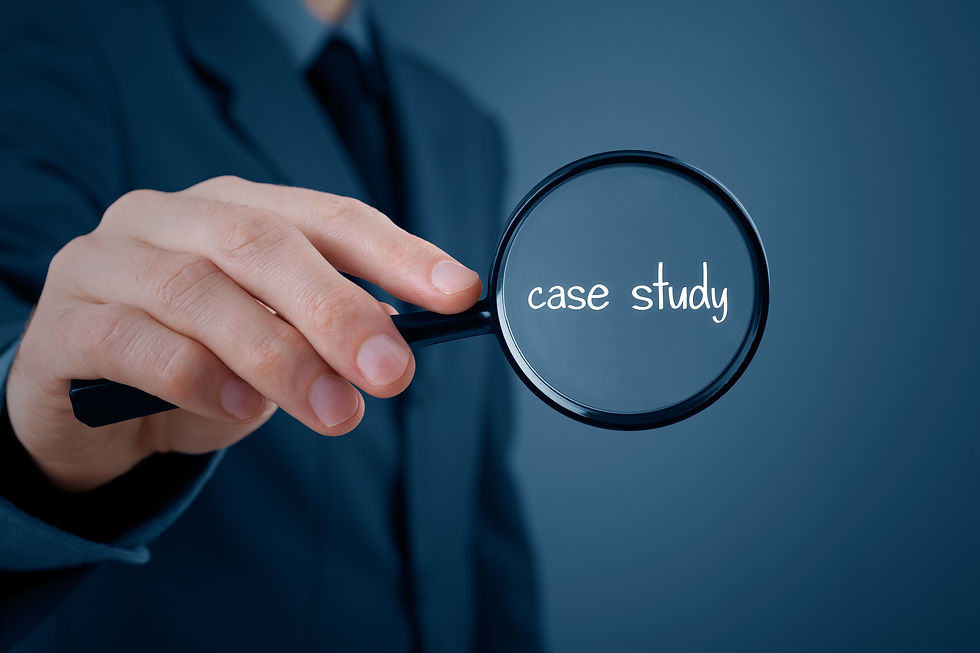